
Ultrasonic Iris
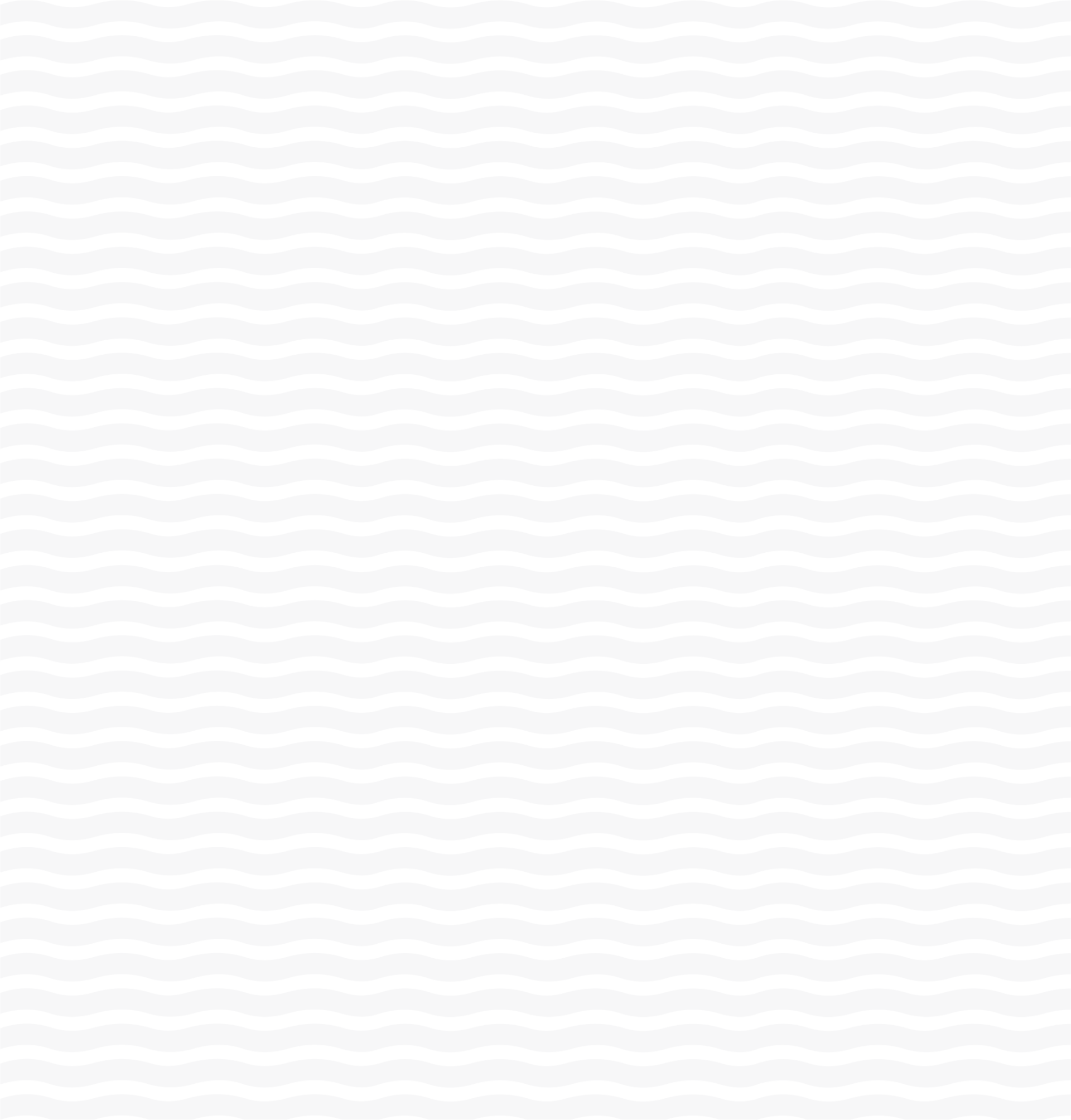
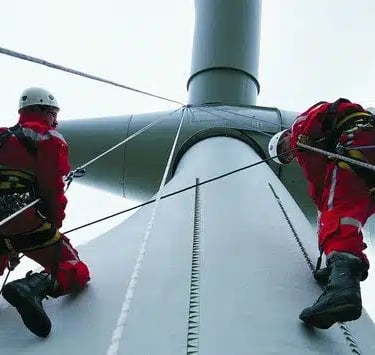
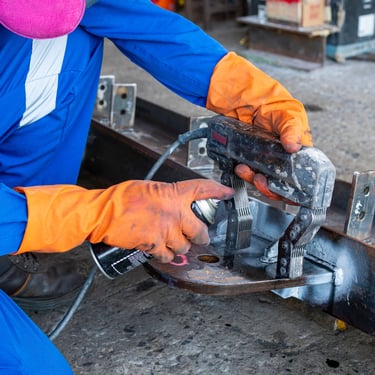
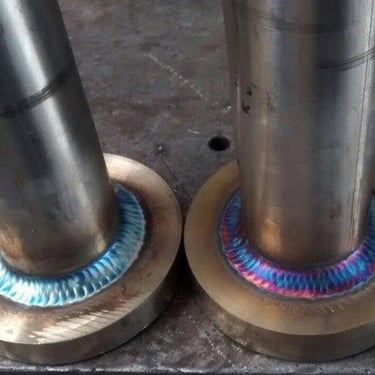
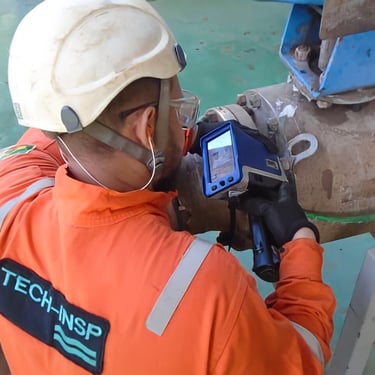
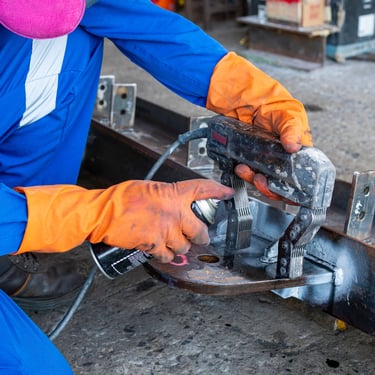
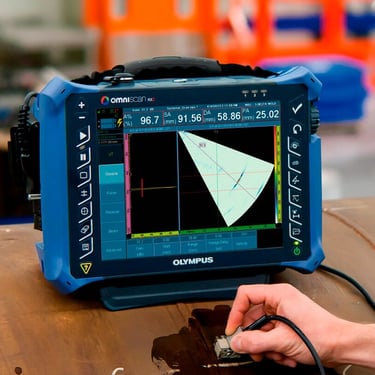
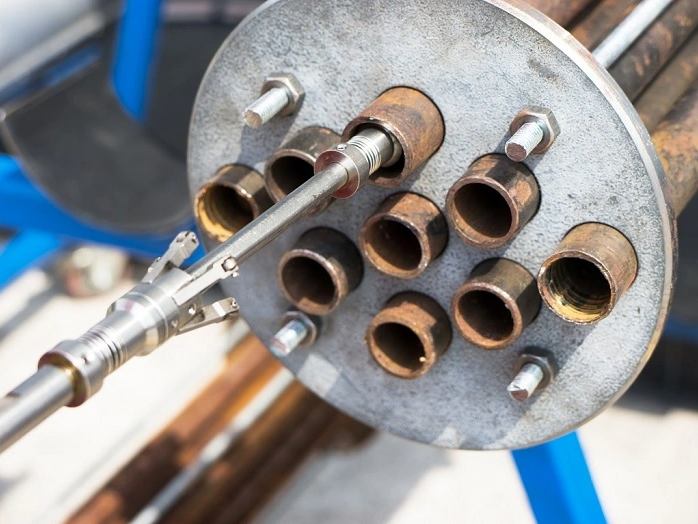
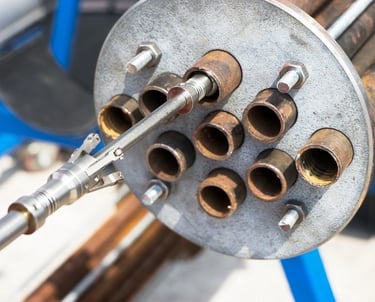
Inspeção IRIS: Um Método Avançado de Avaliação de Tubos
The IRIS (Internal Rotary Inspection System) is a cutting-edge nondestructive testing (NDT) technique designed for the high-precision evaluation of tubes in heat exchangers, boilers, and condensers. This method provides detailed insights into wall thickness, internal and external corrosion, erosion, and other structural anomalies, ensuring the integrity and reliability of critical industrial components.
Probe Structure
The probe is equipped with an ultrasonic transducer capable of emitting a high-frequency sound beam. This beam is directed toward a rotating mirror located inside the probe. The mirror plays a crucial role by reflecting the sound beam perpendicularly to the tube wall, allowing the sound to travel through the entire thickness of the material for precise inspection and evaluation.
Principle of Operation
When the sound beam reaches the tube wall, part of it is reflected back toward the ultrasonic probe. The probe measures two fundamental parameters: the sound transit time, which is the interval between the emission of the beam and the reception of the echo, and the echo amplitude, which indicates the intensity of the reflected sound. With this information, technicians can calculate the tube wall thickness and identify the presence of discontinuities.
Detection of DiscontinuitiesAs descontinuidades que podem ser detectadas incluem:
Corrosion: Material loss on the tube surface caused by chemical or electrochemical reactions.
Erosion: Surface wear due to the flow of fluids or particles.
Cracks: Fractures or breaks in the material structure that may compromise tube integrity.
Holes: Openings that can lead to leaks and structural failures.
Data Generation
As the probe moves along the tube, it generates a detailed thickness profile and a defect map. This data is recorded in specialized software, which allows for visualization and analysis of the results. The software can generate graphs, reports, and images that help engineers understand the condition of the tube and make informed decisions regarding maintenance and repairs.
Vantagens da Inspeção IRIS
Advantages of IRIS Inspection
Accuracy: Ultrasonic technology provides precise measurements of material thickness and real-time detection of discontinuities.
Non-Destructive: As a non-destructive method, the integrity of the tube remains intact during inspection.
Comprehensive Evaluation: Enables a thorough analysis of the entire tube circumference, ensuring no areas are left uninspected.
Data Recording: Results can be stored and analyzed later, making it easier to track the tube’s condition over time.
Conclusion
IRIS inspection is an innovative technique that combines ultrasonic technology with data analysis to ensure the safety and efficiency of piping systems. Its continuous use in industries highlights the importance of maintaining structural integrity and preventing failures, contributing to the safe and cost-effective operation of facilities. The figure below illustrates the principle of IRIS inspection, highlighting the components and functionality of the system.