
Thickness Measurement
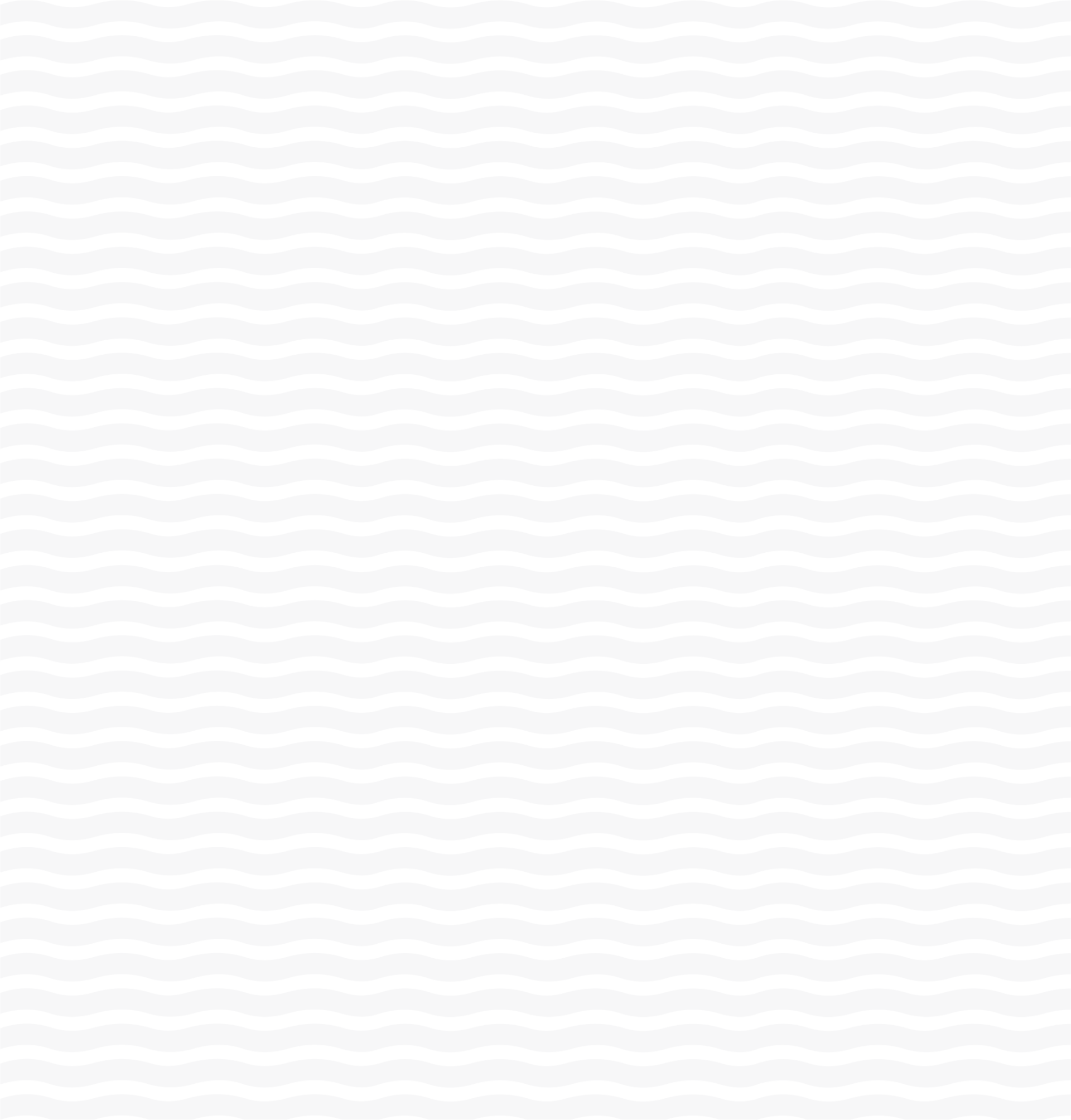
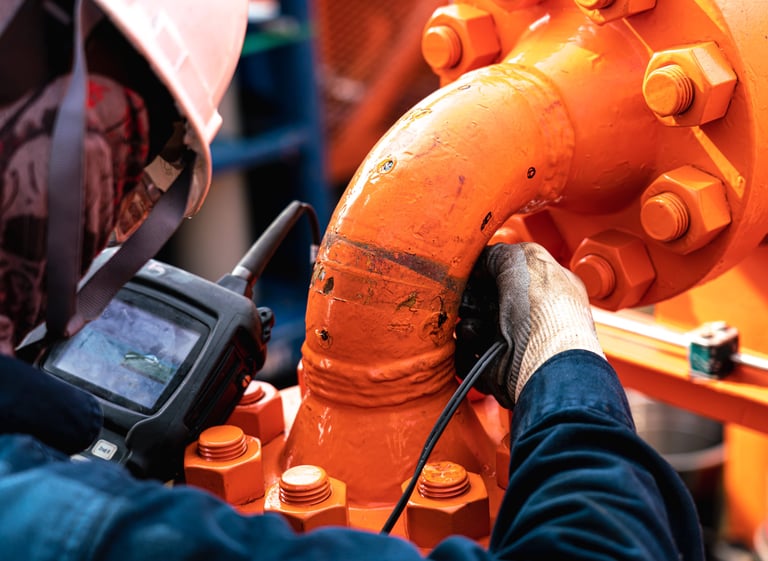
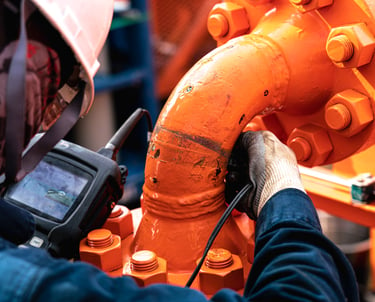
Liquid Penetrant Testing
hickness measurement is a critical process used across various industries to assess the dimensions of materials, components, and structures. It is essential for ensuring the quality, safety, and performance of products and systems, particularly in industries such as construction, manufacturing, aerospace, automotive, and oil & gas.
Thickness measurement provides crucial information about the material integrity, wear levels, and maintenance needs of components that are subjected to environmental factors like corrosion, erosion, or general wear over time. Accurate thickness measurement ensures that materials meet the required specifications and that components function safely under operational conditions.
Methods of Thickness Measurement
There are several methods used to measure thickness, each suited to different materials and applications:
Ultrasonic Thickness Measurement:
This is one of the most widely used non-destructive methods. It utilizes high-frequency sound waves that travel through a material, and the time it takes for the sound to return is used to calculate the thickness. It is highly accurate and can be used for materials of varying thickness, including metals, plastics, and composites.Mechanical Gauging:
In this method, a caliper or micrometer is used to physically measure the thickness of a material. This method is often used for simple and accessible measurements, particularly for thicker, more robust materials.X-ray or Radiographic Measurement:
X-ray or radiographic inspection can be used to determine the thickness of materials, particularly in applications where there is a need to inspect hidden or difficult-to-reach areas. The radiation passing through the material can reveal thickness variations and other structural characteristics.Laser Measurement:
Laser-based technologies provide precise, non-contact thickness measurements. They are ideal for high-speed applications and thin materials, offering high accuracy and speed, especially for surfaces that cannot be touched or accessed easily.Magnetic Induction Measurement:
Magnetic induction is commonly used to measure the thickness of non-ferrous metals such as aluminum and copper. This method relies on the principle that magnetic fields interact differently with materials of varying thicknesses.
Applications of Thickness Measurement
Corrosion Monitoring: In industries such as oil & gas or marine, where materials are prone to corrosion, regular thickness measurement helps track material degradation over time, allowing for proactive maintenance or replacement before catastrophic failures occur.
Quality Control: Manufacturers use thickness measurement as part of their quality control process to ensure products meet industry specifications and standards. This is especially important in industries like aerospace, where even minor deviations in thickness can result in failure.
Structural Integrity: For buildings, pipelines, pressure vessels, and storage tanks, knowing the exact thickness of components is vital for structural integrity assessment. Over time, materials can lose thickness due to wear, which compromises the safety and functionality of the structure.
Advantages of Thickness Measurement
Non-destructive: Many thickness measurement techniques are non-destructive, meaning they don’t alter or damage the material being measured. This is important for maintaining the integrity of sensitive or expensive components.
Accuracy and Reliability: Modern measurement methods provide highly accurate and repeatable results, ensuring that industries can make data-driven decisions regarding maintenance and operation.
Cost-Effective: In many cases, measuring thickness is a cost-effective way to ensure quality control, minimize downtime, and prevent costly repairs by identifying potential issues before they escalate.
Conclusion
Thickness measurement is a crucial process in maintaining the safety, reliability, and efficiency of materials and components. By employing accurate and reliable methods, industries can ensure the structural integrity of critical assets and reduce the risk of costly failures or accidents.
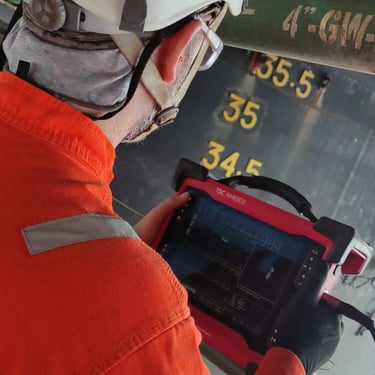
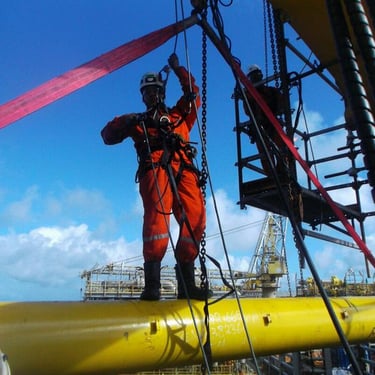
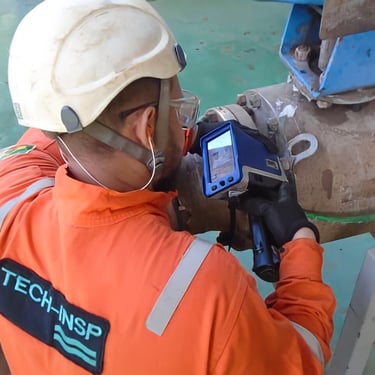
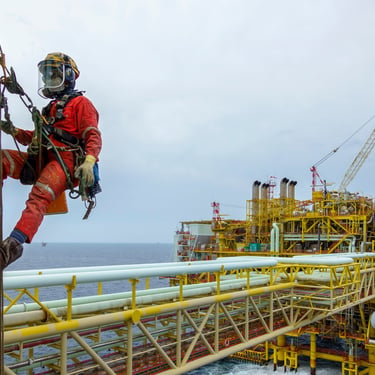
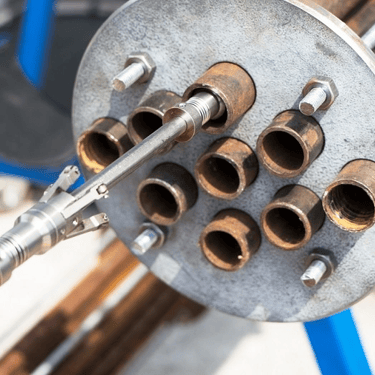
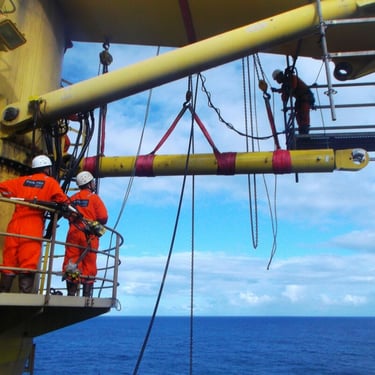